Published
by Rogers Corporation
Elastomeric Material Solutions
How Do I Choose the Right Silicone Material for My Application?
Selecting a suitable silicone material for your application is a critical decision that can significantly impact the performance and longevity of your product. Whether you're working on a sealing gasket, electronic component, or a different application, choosing the right silicone material is paramount. In this guide for engineers, we'll walk you through the top six considerations to help you make an informed decision.
Want to see a visual summary of the advantages?
Top 6 Silicone Design Material Selection Considerations
-
Temperature Exposure
In which temperatures will my material operate? What are the maximum, minimum, and typical temperatures?
- When selecting a silicone material, temperature exposure stands out as a pivotal consideration as it directly impacts application performance and longevity.
- Choose a silicone material with the appropriate temperature resistance rating that aligns with your application's operating conditions. This will ensure optimal material performance and durability in your application.
- You want to consider a few different temperature parameters in your application: temperature range (maximum and minimum) and typical operating temperature.
- In the case of Rogers BISCO® silicone cellular foams, the continuous temperature range spans from -55 °C to 200 °C, with intermittent temperature tolerance extending up to 250 °C for short durations.
- Always check a material's Technical Data Sheet to find its respective temperature parameters.
-
UV/Ozone and Radiation Resistance
Will my material be outdoors and/or exposed to UV, ozone, and/or radiation?
- Silicone is resistant to radiation, oxygen, ozone, and UV light (A, B, and C wavelengths). The silicon-oxygen bonds in silicone's inorganic chemistry are more stable than those between the carbon atoms in organic polymer chains. The amount of energy provided by UV light is high enough to break Carbon-Carbon bonds, but not enough to damage silicone's Si-O bonds.
- Silicone's resistance to radiation, oxygen, ozone, and UV makes it a great option for outdoor applications where these harmful environmental conditions naturally occur and degrade other materials.
- This same resistance is also why silicone can be sterilized for many medical and life science applications using gamma ray and electron beam radiation, Ethylene Oxide Sterilization (ETO), or traditional Autoclave Steam Sterilization.
-
Flame Resistance:
Is fire safety important in my application? Does my material need to meet any flame ratings?
- In applications where fire safety is a concern, engineers should consider a silicone material that meets one of the following industry-recognized flame ratings:
-
Chemical and Fluid Resistance:
Will my material be exposed to any chemicals or fluids?
- This is an important consideration if materials come in contact with chemicals or fluids during cleaning or other scenarios.
- Generally, silicone materials have good resistance to chemicals, fuel, and oil at temperatures that would otherwise eliminate most other elastomers from being used in an application (except for fluoroelastomers). You may need to use a fluorosilicone material if high chemical resistance is required.
- If silicone encounters chemicals or fluids, the material may show some swelling. Once the material is removed from the fluid, it returns to its original shape and shows little loss of its properties.
-
Outgassing:
Is my application sensitive to contamination?
- There is always a concern about what potentially can outgas from a material. BISCO silicone cellular foams are formulated and are post cured, reducing the available outgassing components to levels in the ppm (part per million). This allows them to be used in electronics since there are very low levels of contaminants that can cause interference with the components.
-
Budget
What is my budget?
Can a high-quality material help me prevent application failure, injury, and uphold my reputation?
- While silicones can be more expensive than many other elastomers on the market, evaluating the risk and reward the material provides is a good idea.
- Can you risk a failure in the field, which can cost thousands of dollars in warranty claims?
- Can you risk a preventable injury due to your device?
- Can you risk your reputation in the market?
Read more about the hidden benefits of silicone.
Key Points
Selecting the right silicone material for your application involves carefully assessing multiple factors, including temperature exposure, UV/ozone resistance, flame resistance, chemical resistance, outgassing, and budgetary considerations. Engineers should prioritize the specific requirements of their projects and make informed decisions to ensure optimal performance, durability, and safety.
By following these guidelines, you can more confidently choose the ideal silicone material for your application and contribute to the success of your project.
Additionally, you can rely on Rogers’ dedicated Technical Service and Development Team to provide material selection guidance based on your application requirements.
Contact your Rogers Sales Engineer and take the first step towards confidently choosing the right material for your application. #RelyOnRogers
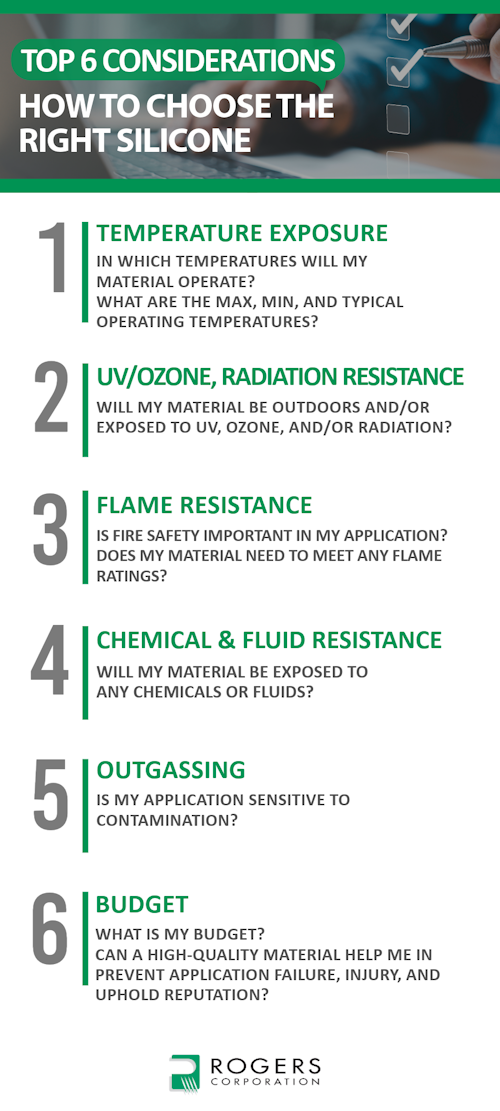
Related Blogs
Published on Feb 09, 2024
Return to Blog